The Evils of the Attic – Structural Ventilation Solution
The Start (and End) of the Marriage
The structure and HVAC system are joined during initial construction. The structure is intended to create a shelter and the HVAC system is to keep the inside temperature at 72°F±. Both succeed in reaching their goals!
And, they reached their goals but damaged each other.
The attic was vented with humid outside air, as in many structures.
Throughout the structure, in order to have plumbing, mechanical, and electrical chases and bold architectural features, single and double walls with cavities are installed. Unfortunately, the cavity walls extend to the attic where humid outdoor air ventilates the area. This humid air enters the cavity walls allowing humid air to flow between walls and through floor cavities. When exposed to the cool indoor wall, floor, and ceiling surfaces, the humid air condensed inside the cavities allowing mold to flourish.
And, when the mold escapes into the living space, the HVAC system spreads the mold throughout the mechanical units, ductwork, supply ducts, return ducts, and throughout the house.
The result is a structure and HVAC system that work in harmony to effortlessly grow and distribute mold throughout the house and mechanical system. Mold damage becomes widespread. Engineered wood products are damaged by condensation and elevated humidity.
Time to start over.
Consider these structural ventilation solutions.
Solution 1 without Structural Ventilation – Put it Back the Way it Was
During mold remediation, the mechanical systems are cleaned, if possible, or replaced. The damaged structural components are replaced. The entire structure is cleaned and is certified to be mold free.
So if we put it back the way it was, we repeat the start (and end) of the marriage.
This is not a good solution.
Solution 2 without Structural Ventilation – Stop Humid Airflow from the Attic
This is actually a great solution. If we seal every opening that can allow humid attic air from entering the cavity walls, problem solved!
Actually, we can minimize the airflow, but we can’t stop it. Openings include large open cavities, openings at gas, water, and sewer piping, openings at electrical conduits and wiring, and an endless supply of framing separations.
So, this solution can minimize the problem, but not solve it.
Solution 3 without Structural Ventilation – Air Condition the Attic
This is actually a great solution, too. If we replace the attic air with conditioned air, and allow the attic and interior space to circulate the same air, problem solved!
To make this work, we need to insulate the attic roof between rafters with spray foam. Insulation at the floor of the attic is not necessary. Openings between the attic and interior space can remain.
But, the building envelope is not airtight. Airflow through the building envelope is typically the biggest contributor to “fresh” outside air inside the building. It is considered “fresh” because it flows through the nooks and crannies of the building envelope that is typically not considered “clean”.
And when the humid outdoor air travels through the building envelope and contacts the cold interior finishes, humidity rises, condensation occurs, and mold infestation and structural damage recur.
This solution is actually very good, but incomplete.
Solution 4 without Structural Ventilation – Air Condition the Attic and Seal the Structure
This is Solution 3 with improvements.
Sealing the structure entails the use of spray foam insulation in exterior walls instead of fiberglass insulation. In addition, the building envelope is sealed with Aeroseal to significantly reduce air leakage. The HVAC no longer has to control indoor humidity created by outside air infiltrating the structure.
When this is done, the HVAC system is required, by the Building Code, to supply outside air into the structure. There are variations to the methods. In my opinion, the following requirements should be met to ensure benefits are made:
a. Supply continuous outside air at a rate of 0.10 cfm/square foot of floor area
b. Condition the outside air to the necessary temperature and humidity before supplying to the conventional HVAC system
c. Supply the air into each area and into areas enclosed with doors
d. Supply the air under positive pressure to further minimize outdoor air infiltrating into the structure
This is a preferred solution.
Solution 5 – Structural Ventilation of the Building Envelope
More information at this link.
This is Solution 4 with improvements. The air supplied to the building for interior comfort, at the required temperature and humidity, is circulated as necessary. This air is then exhausted into the building envelope where it is circulated and exhausted to the exterior. This results in:
- Improved indoor air quality by ensuring conditioned filtered outdoor air is supplied for to the structure for improved respiration and controlled room temperature and humidity.
- Minimize moisture, contamination, and deterioration of the building envelope by allowing air exhausted from the interior to flow through the building envelope.
- Reduce energy costs by allowing the air flow through the building envelope to minimize thermal and moisture flow between the exterior and interior. Thermal resistances of the walls and windows are increased by a factor of 3. The thermal resistance of the attic, typically the largest contributor of heat gain and loss, is increased by a factor of 5.
The pilot structure is being designed and will be built soon. Although the best solution, it’s not ready for distribution. In the meantime, Solution 4 provides the cleanest and most enduring structure in harmony with the HVAC system.
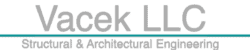
Vacek LLC, formerly Vacek Group, is a Houston area structural and architectural engineering company established in 1994. The company offers years of experience to insurance companies, attorneys, architects and the private sector.
